大型零部件高压铸造过程中,流动通道复杂,边角结构越多越容易导致金属充型过程中无法良好填充,甚至出现紊流,从而导致内部严重的缺陷,甚至会带来杂质和氧化皮风险。或者由于流动性不足或者多处流动进度不同,从而出现多处金属液面冲击融合,从而导致零件失效。
排气结构需合理设计,仿真技术+过程控制防止气孔产生。模具中原有的气体+金属液流自身带入的气体+包含金属中的气体需要排出,需要在设计之初通过合理的排气结构来排出气体,甚至采用惰性更好的气体保护和一定的真空技术来实现模具中的气体排放,需要大量的仿真技术和生产过程的控制接入,排气过程如果做不到位零件会有大量的气孔产生。
真空压铸法是通过在压铸过程中抽除压铸模具型腔内的气体而消除或显著减少压铸件内的气孔和溶解气体,从而提高压铸件力学性能和表面质量的先进压铸工艺。高真空和超高真空压铸工艺目前在大型一体化压铸件生产过程中有广泛的应用。
行业内定义:高真空压铸是指压力介于50~100 mbar,超高真空压铸则指压力低于50 mbar。一体化压铸要求压铸环境为30 mbar以下的超高真空。
大型一体化压铸件由于其本身型腔的超大体积,对流动成型有巨大挑战,因此对模具的流道和排气设计、模具的加工质量、真空控制、模温控制等各方面都有特定的要求。上述的每个因素也直接影响真空的效果和压铸件的质量。
AnyCasting软件的多阶段真空仿真模拟技术,能够模拟上述各因素在压铸过程中的作用,为用户提供可靠的技术支撑和保障。
韩国AnyCasting软件公司与瑞士方达瑞公司分别代表了铸造模拟软件技术和真空科技领域的前沿开发者。此次两家企业的研发团队联手,对真空压铸模拟两相流耦合求解技术进行了深入的合作与开发。
真空压铸过程的两相流耦合模拟仿真,计算金属熔液和模具型腔中气体在互相作用、彼此影响下的流动形态。
具体来说,对于金属熔液,需分析在特定的流道和排溢系统设计的模具中,根据冲头进程的工艺条件,计算金属熔液充填、氧化夹渣、气体包卷等结果。
对于型腔中的空气,需分析在真空设备和模具为整体的系统中,根据抽真空的起止时间、流量等工艺条件设定,计算气流的速度、压强、密度、模具间隙及设备管路的漏气、达到目标真空度所需的时间等结果。
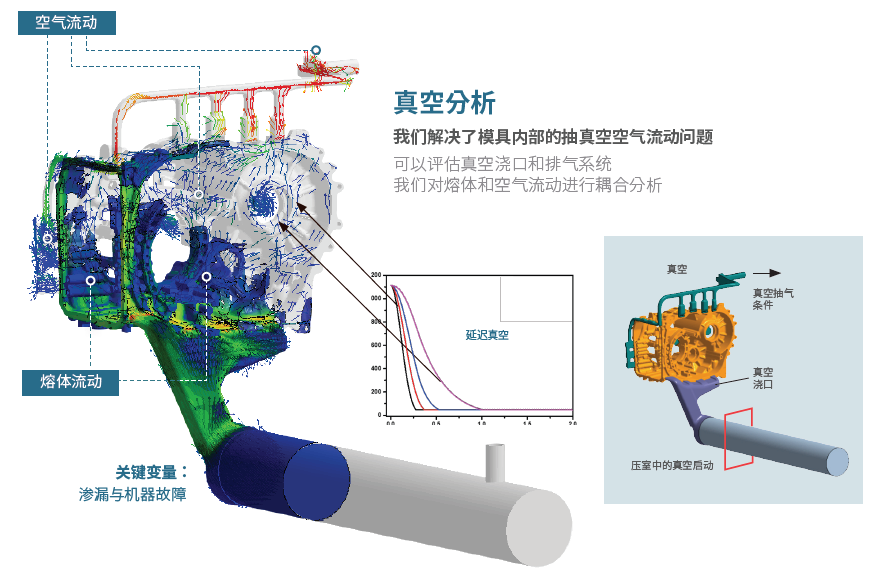
对于真空设备,AnyCasting软件评估包括抽真空设备类型、真空罐、真空泵在内的整个系统抽真空的能力,考虑压室、模具间隙及设备管路的漏气,计算两者之间的平衡。

在此基础上,AnyCasting软件求解型腔中达到目标真空度所需的时间,以及在特定时间下系统能够达到的真空度。用户可以根据上述仿真分析的结果,来优化真空设备类型和规格的选择。
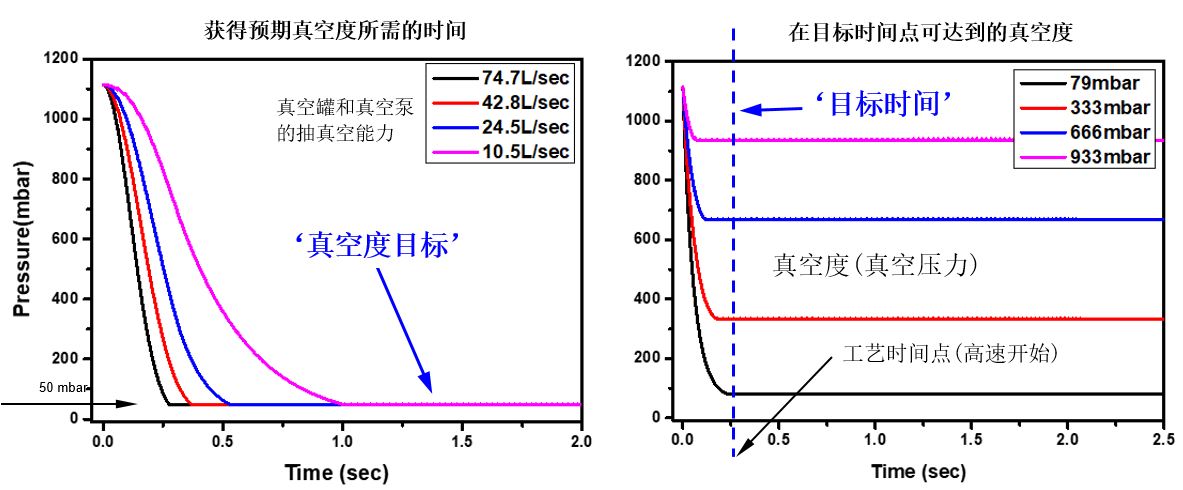
某一新能源汽车电池壳体件,采用抽真空压铸工艺。通过AnyCasting软件,模拟使用不同抽真空能力的设备,模具型腔内空气压力的情况。
铸件及模具:
电池壳体,材料Sliafont 36,重量46 kg,3,300 ton 压铸机
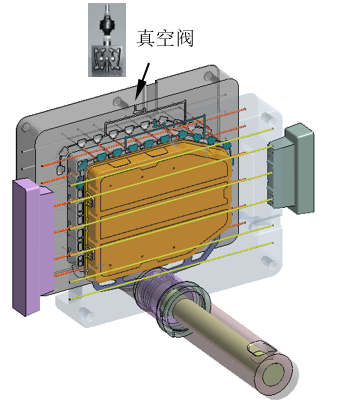
真空设备及工艺:
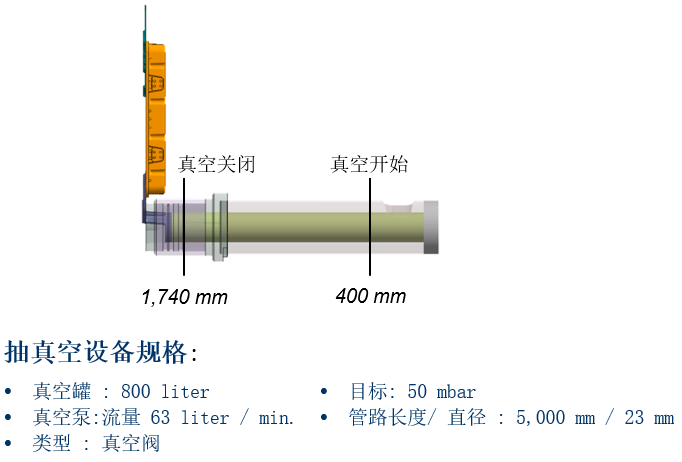
通过AnyCasting软件两相流耦合分析,获得使用不同规格真空设备情况下的各结果:
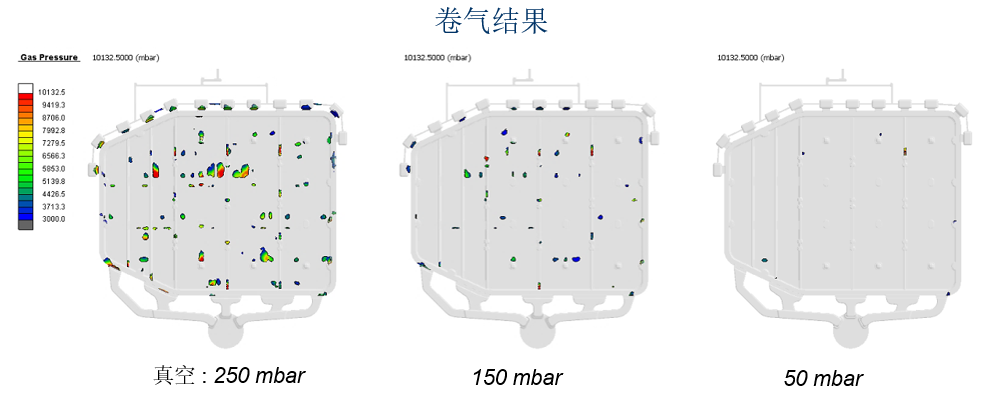
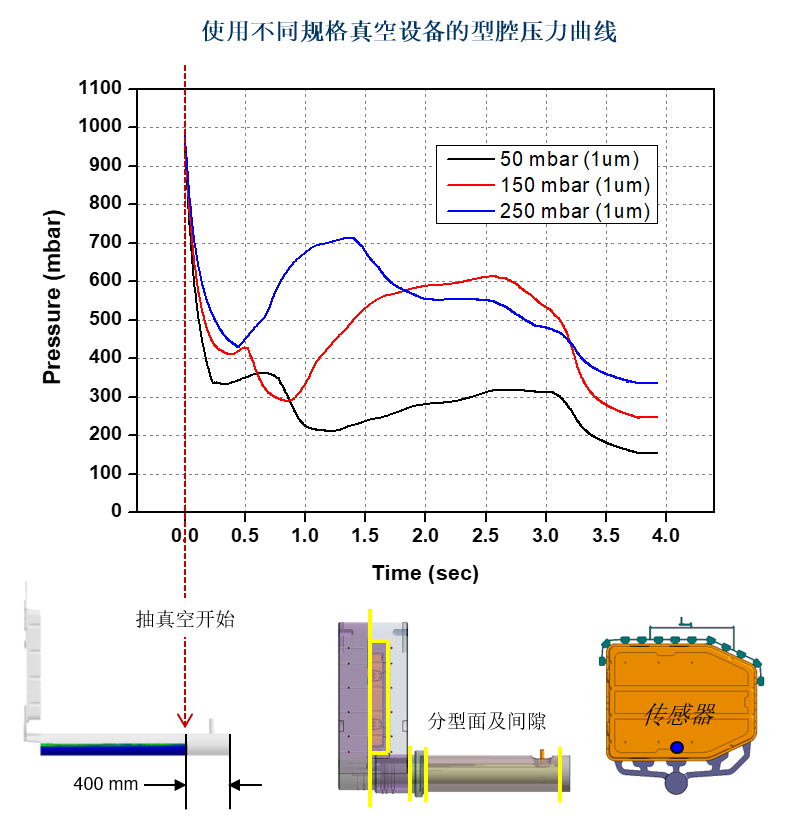
使用两相流耦合求解技术,确保大型压铸件仿真流态精确度可用以评估真空设备和系统,包括真空罐、真空泵、真空阀、模具间隙、压室和管路系统的抽真空能力分析真空迟滞现象,计算达到特定真空度所需的时间,或者在特定时间点型腔可达到的真空度。
AnyCasting的仿真可以为用户在大型一体化压铸件的模具设计、真空设备选择和工艺方案设计提供强大的技术支持。