沈阳机床银丰铸造有限公司是亚洲范围内规模较大的专业化铸造企业之一,产品主要面向机床工具、风力发电、通用机械、船舶、矿冶和汽车等领域。在大型铸件的工艺设计和生产过程中,数值模拟分析技术的应用为企业大大降低了试制试错的成本,缩短了研发周期,是优化生产工艺、提高铸件生产质量必不可少的技术手段之一。
在2653251Y-滑块技术攻关项目中,原有的生产方案(图1)采用底注式流道以及普通冒口补缩方案设计,存在着以下的铸造缺陷:导轨1、导轨2以及固定孔处出现缩孔缩松问题,如图2所示:
初始工艺方案:
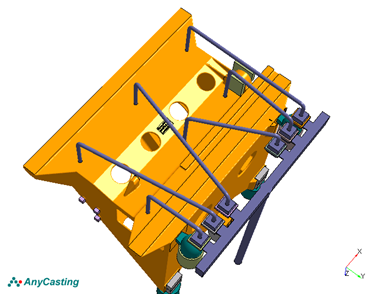
图1 初始工艺方案
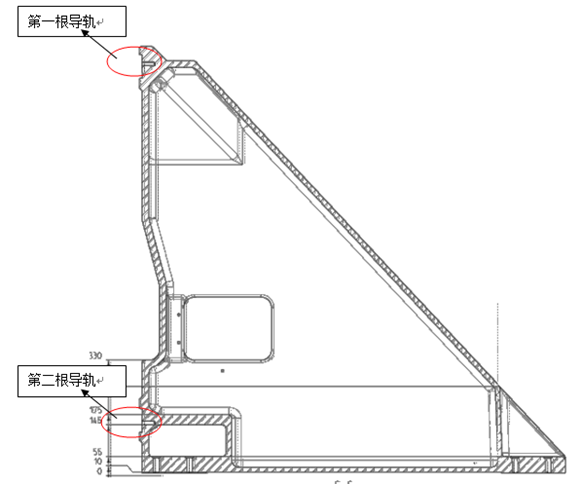
图2 原始工艺方案存在的铸件缺陷
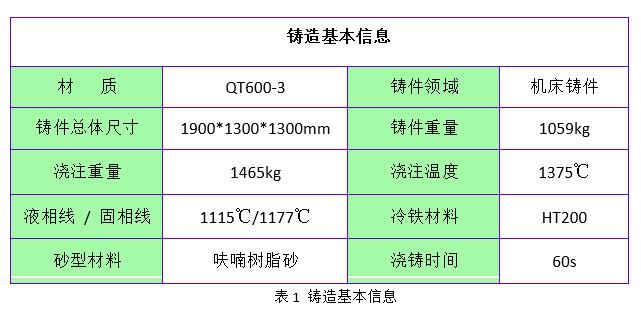
表1 铸造基本信息
AnyCasting软件的模拟,再现了原方案凝固顺序中产生的缺陷,为优化工艺设计提供了判断依据:
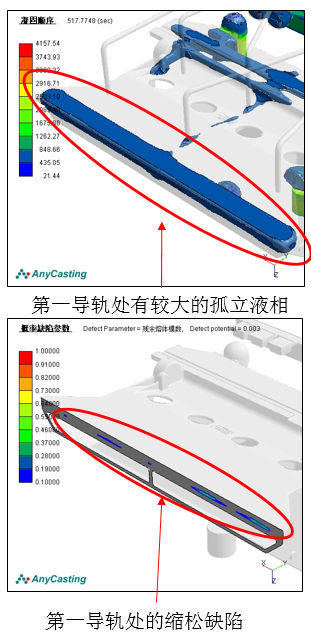
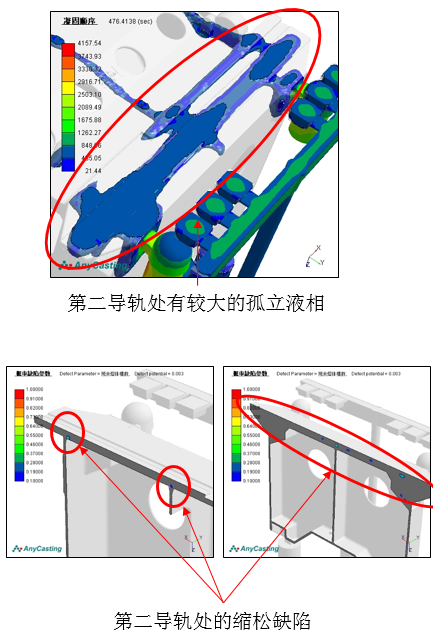

分析显示,原方案中顶部冒口加冷铁的方案对补缩不利,我们尝试将普通冒口改为发热冒口并将位置下移调整。同时,通过在两导轨处增加冷铁来改善凝固顺序。改进前后的工艺方案对比如下图所示。
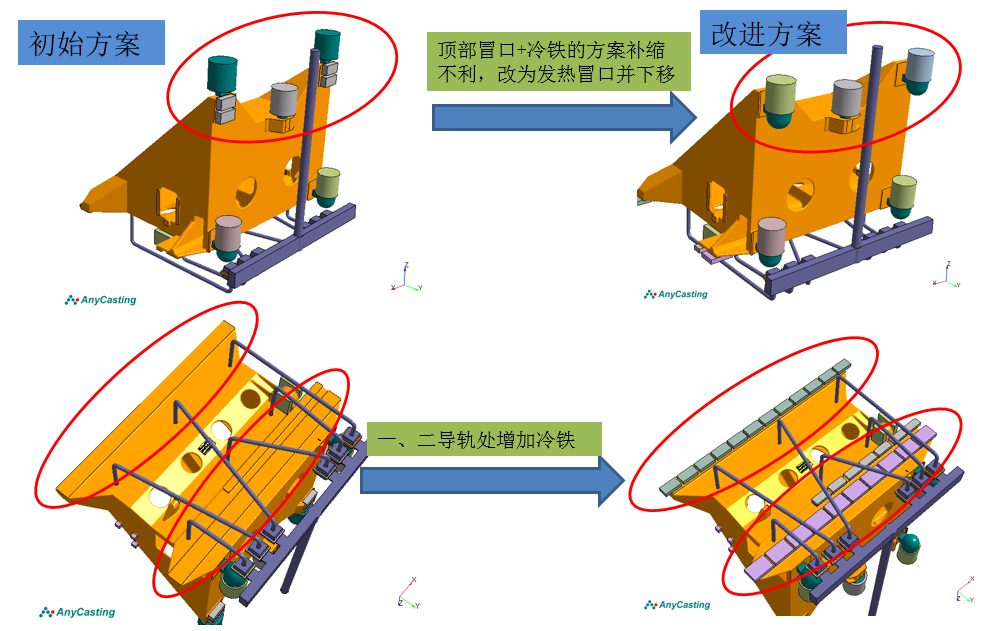
对于改进的浇冒系统,我们再一次运用AnyCasting软件进行仿真分析,分析的结果显示,导轨1、2处的孤立液相区域由于冷铁的作用,明显减小,基本可以消除缩松缺陷。固定孔处发热冒口的补缩作用非常有效,不再有孤立液相存在,完全消除缩松缺陷。分析结果截图如下图所示。

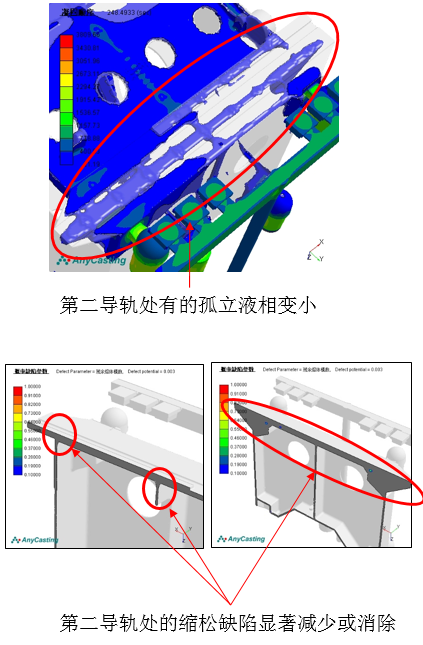

但是,对于优化方案的模拟分析同时也预测到,因为加了冷铁,导轨处的充型温度较低,产生冷隔缺陷的风险较大,所以建议在实际生产过程中,需注意适当提高浇铸温度

总结:
通过数值模拟仿真软件AnyCasting的应用,2653251Y-滑块工艺得到了优化,铸件生产质量明显改善。由此可见,铸件充型及凝固过程数值模拟对指导解决铸造工艺过程具有重大的实践意义,是提升传统砂型铸造水平的新技术。通过此项目,我们可以得出以下结论:
1)Anycasting软件能够实现球铁铸件充型及凝固过程模拟,在产品工艺设计时,能够对工艺方案的选择提供判断依据,缩短新品研制周期。
2) 通过预测缩孔缺陷主要存在位置,可以优化铸造工艺,为产品质量快速提升提供帮助。