案例分析 | 实验拟合 精确输入
大型铸钢件:汽轮机壳体
我们常说,Garbage in, garbage out!(垃圾输入,垃圾输出)确认模型参数的准确性对模拟结果的成败至关重要。我们今天想通过韩国斗山重工大型铸钢件模拟仿真的案例分析,为大家提供一种模拟仿真与实验拟合相结合的思路。
铸钢件凝固收缩大,铸造工艺复杂。为了保证一次浇注、一次成功,韩国斗山重工在大型汽轮机壳体的铸造工艺设计中,采用AnyCasting铸造模拟进行预判分析和研究。
铸件分析
本案例汽轮机壳体铸件,为下图汽轮机的下壳体。
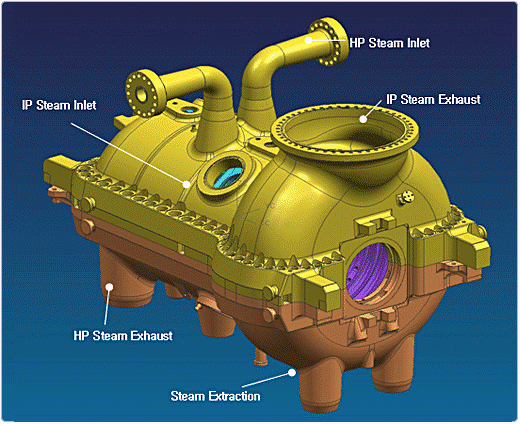
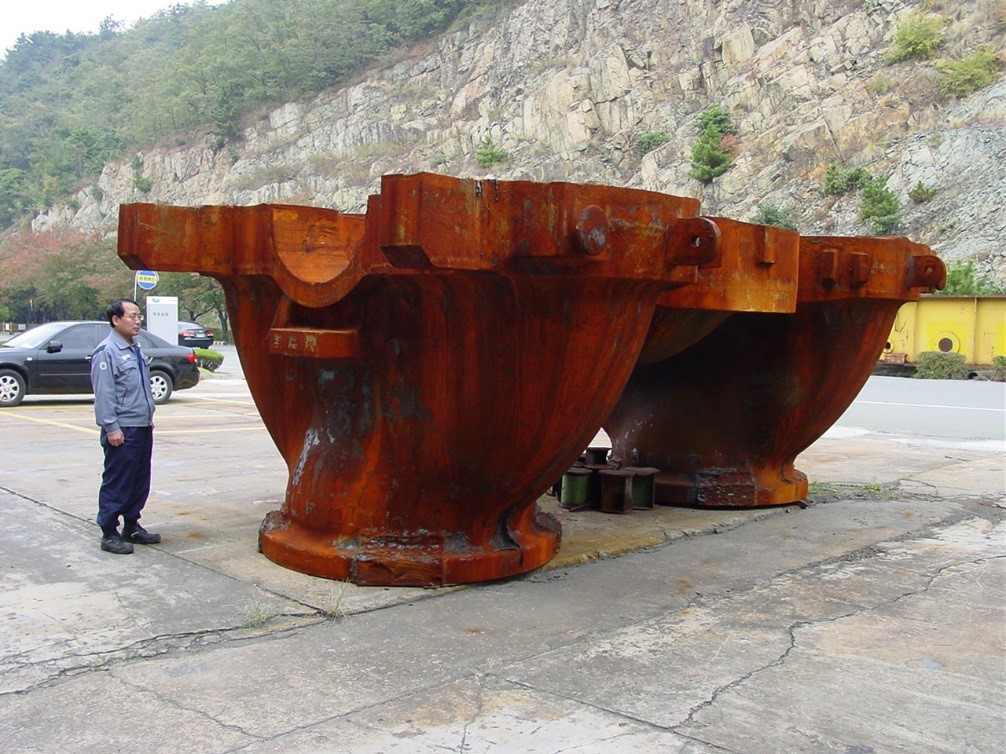
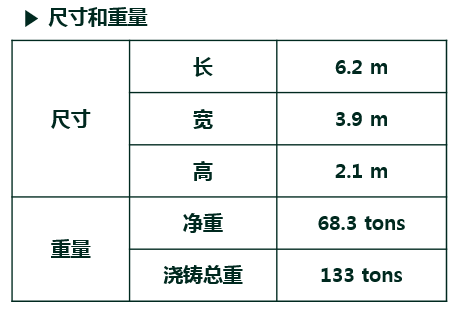
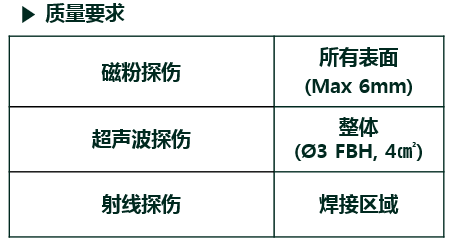
以上数据显示,铸件尺寸大,且质量要求高!
仿真的必要性
实践证明,模拟仿真可以:
1. 减少铸造过程的试错风险;
2. 预测复杂形状铸件的凝固顺序;
3. 预防重大铸造缺陷;
4. 节约能源和材料,并优化铸造工艺设计
仿真的策略
STEP 1:简单试件 – 传热系数的获取和验证
本案例中,由于对铸件收缩缺陷的要求高,因此模拟仿真过程前,首先要验证保温冒口传热系数的准确性,以确保补缩效果仿真的准确性,从而获得准确的收缩缺陷预测。斗山重工通过埋设热电偶的浇铸实验和模拟仿真实验验证拟合的方式,获得了一手的关键数据!实验的模型如下图所示。其中,#1型腔不使用保温套,#2使用1层保温套,#3使用2层保温套。
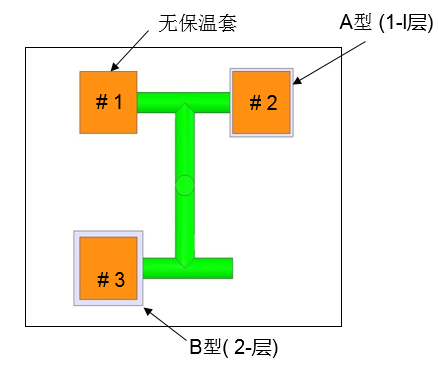
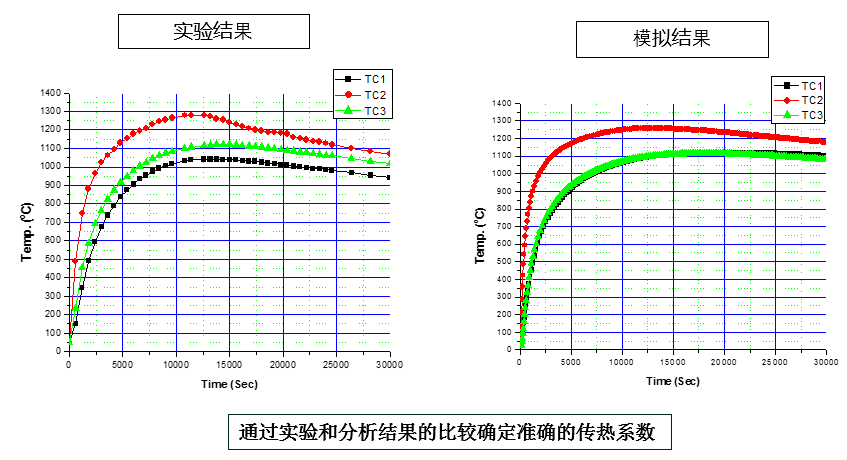
STEP 2:铸件产品的凝固分析
由于铸件产品形状较为复杂,斗山重工先单独对产品进行了凝固分析,用以发现产品的凝固顺序,找到凝固缺陷的位置,并计算和设计冒口的位置和大小。
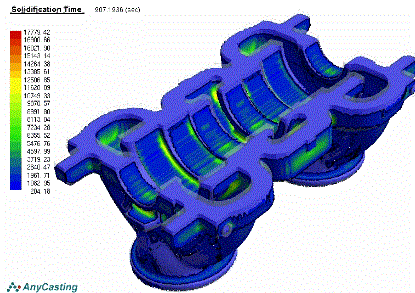
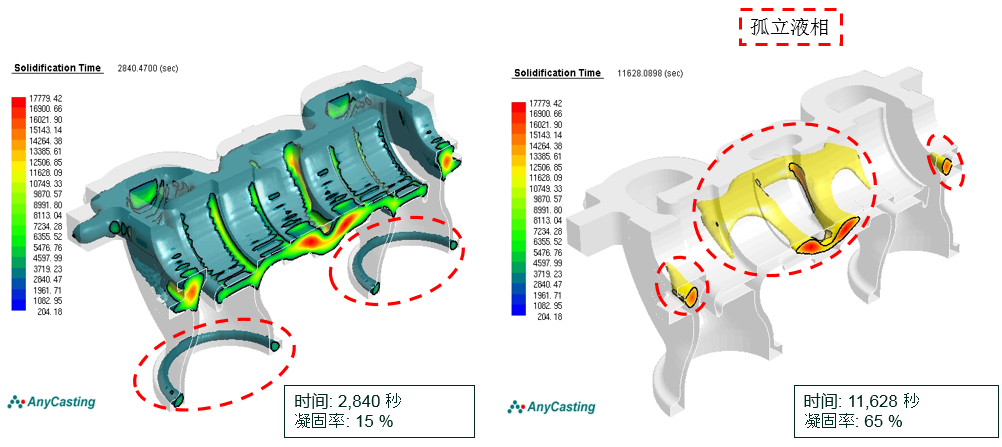
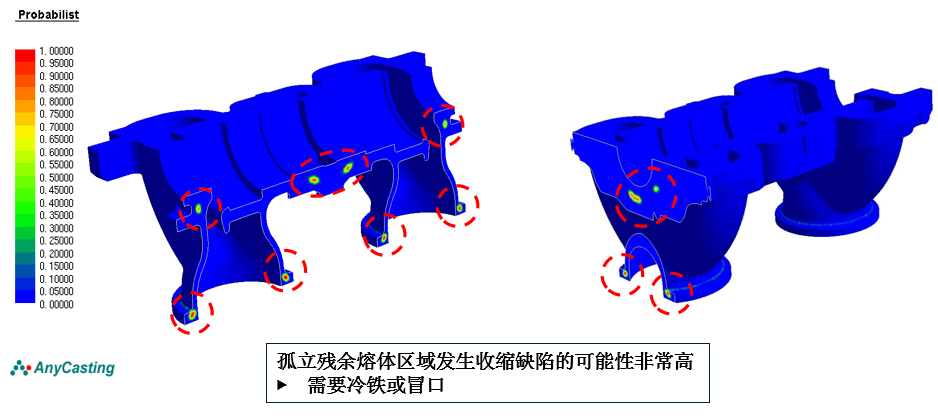
STEP 3:整体浇铸系统分析和优化
在找到热节点和收缩缺陷位置后,工艺设计人员完成了整体的浇冒系统设计。回到模拟软件中,再对整个铸造系统进行包括流场、温度场和凝固分析在内的耦合计算,并对结果进行分析和改进。此前在STEP 1中获得的传热系数,用于模拟保温冒口的补缩过程。

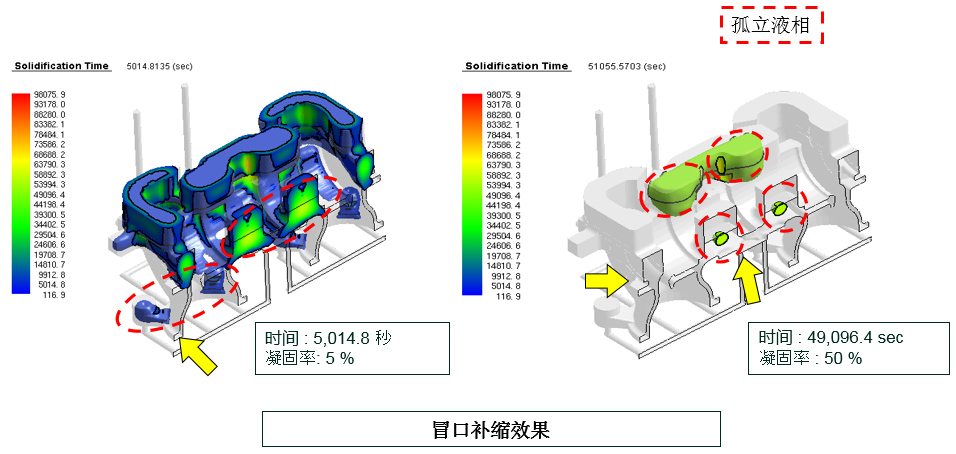
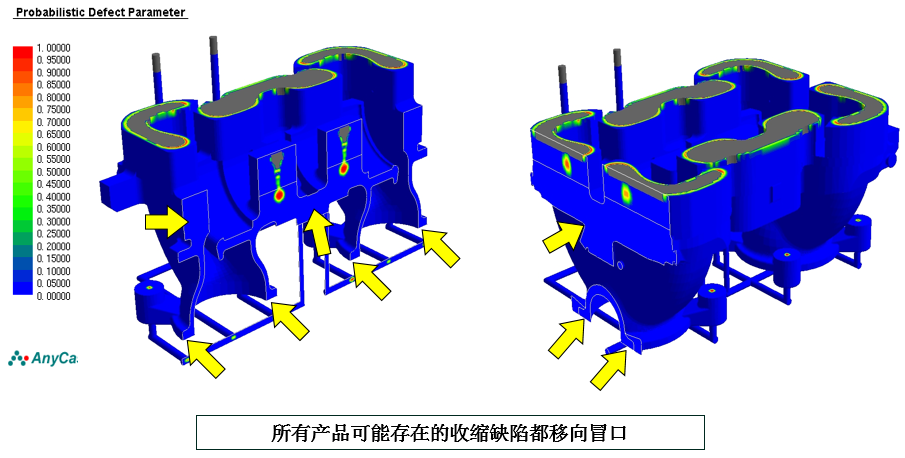
在得到上述结果的基础上,工艺方案被进行进一步改进和优化,直至分析预测的结果能够被完全接受,才将方案固定下来。
STEP 4:产品制造和检验
在AnyCasting模拟软件的技术支持下,技术团队在计算机中验证了多种不同的工艺设计方案,汽轮机壳体达到一次浇注一次成功的目标。计算机模拟仿真对于大型件和复杂件来说,是必不可缺的技术工具。
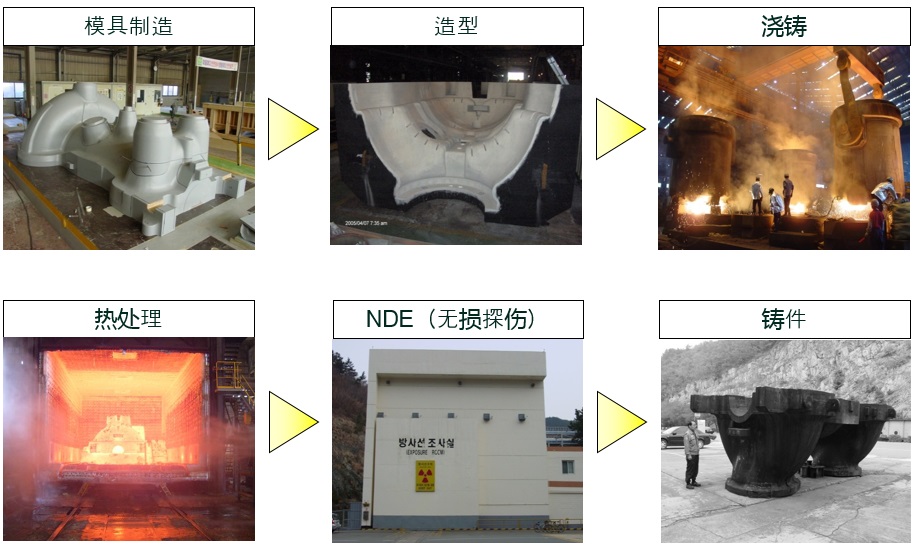
总结:
通过斗山重工对大型汽轮机工艺设计过程的介绍,我们了解了大型铸钢件模拟仿真的策略。为了获得与企业生产相吻合的分析参数,用户不妨可以采用简单试件实验与仿真实验相互验证拟合的方法。此外,从凝固分析->浇冒系统设计->流动凝固耦合分析->优化设计和分析的仿真策略,也值得大型铸钢件用户参考和运用。